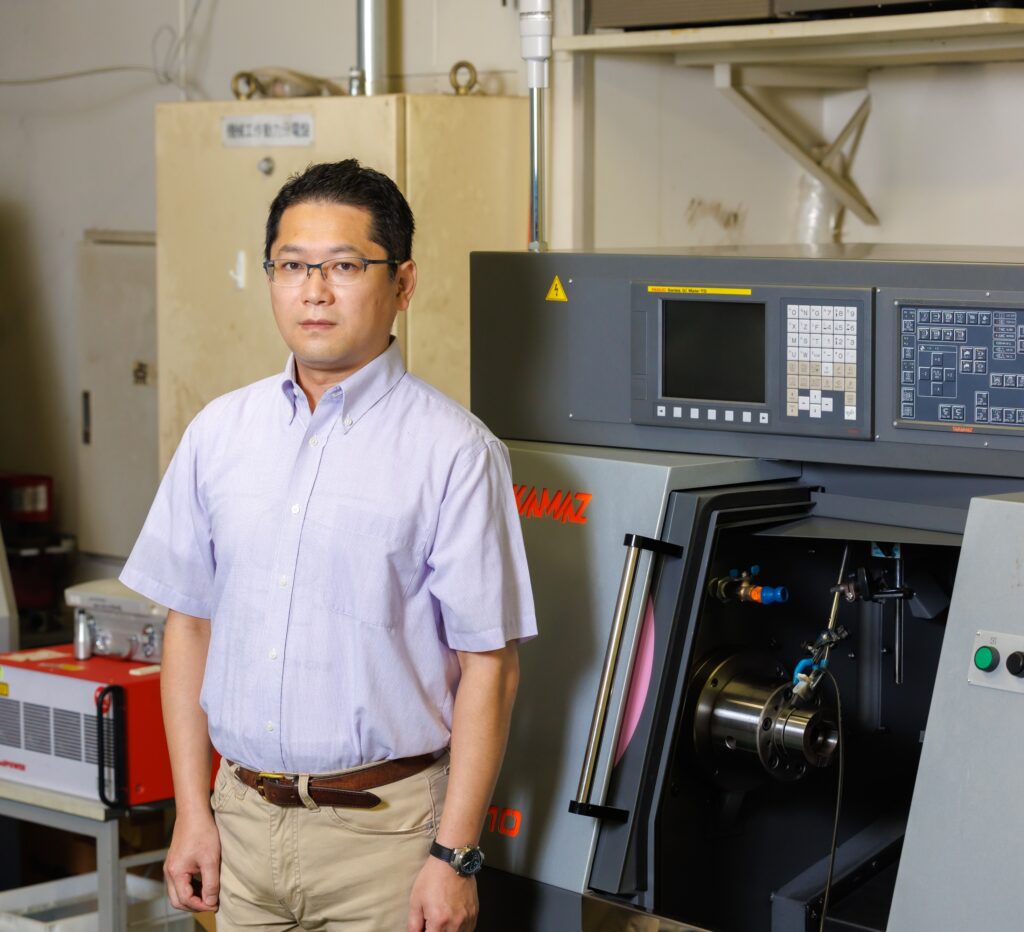
Associate professor Hidetake Tanaka from the Faculty of Science and Technology undertakes development of material processing techniques with added value from the perspectives of manufacturing process, measurement and functionality assessment in precision engineering. He currently focuses on research about machining methods for carbon fiber reinforced plastics (CFRP), which is being applied to increasingly more fields.
I undertake research about CFRP, which is a composite material with increased strength from combining plastics with carbon fibers. Lightweight yet similar in strength to steel, it is used as a material in a wide range of industrial fields, from aerospace to sporting products. Its application scope grows with the advancement of its functions, and currently, approximately 50% of the latest aircraft body materials use composite materials that contain carbon fibers.
Meanwhile, given its hardness, carbon fiber is difficult to cut, and an issue of CFRP is the severe tool wear during cutting. Usually, molding techniques are used for forming CFRP, and machining is required only in certain processes, such as trimming, creating holes, and finishing.
Even so, in recent years, there has been an increase in cases where composite materials containing carbon fiber are used as materials for small parts. There is growing demand for precise machining, and various companies and universities are conducting research and development of manufacturing methods.
Advocating new machining methods by combining conventional techniques
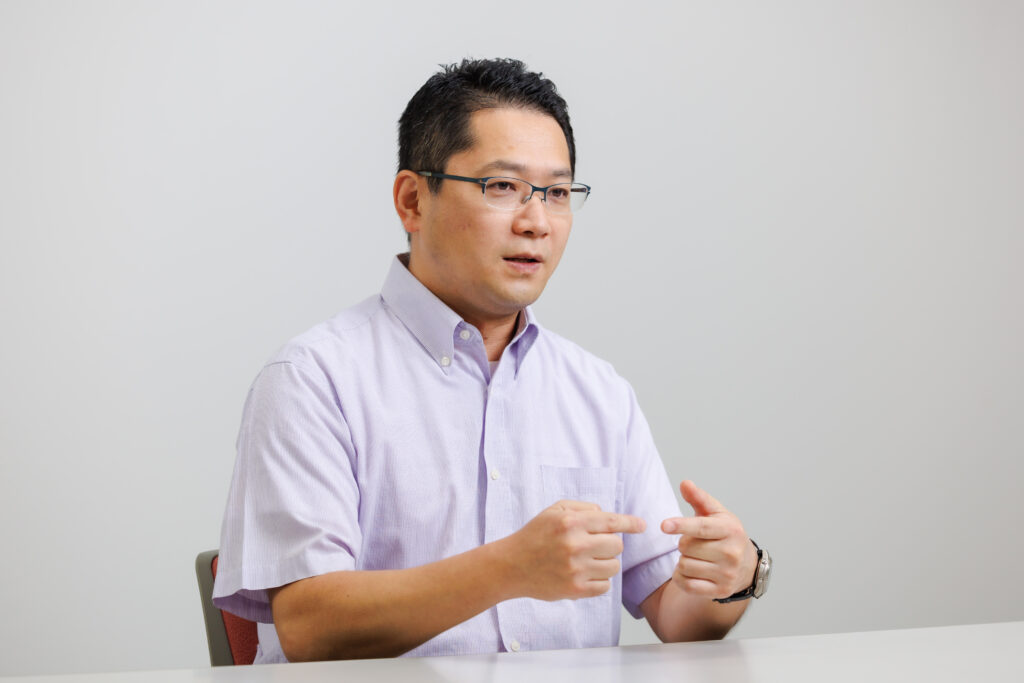
For efficient cutting while reducing tool wear, methods that coat the blades of cemented carbide tools with ceramic or diamond—materials that are resistant to wear and peel—or electric discharge machining (EDM) that uses electrical energy are usually used for machining CFRP.
In contrast, electric discharge-assisted turning (EDAT)—which I am jointly researching and developing with the cooperative company —is a hybrid processing method that selectively cuts carbon fiber using electric discharge, then removes the remaining plastic and cut carbon fiber with turning tools.
It is different from conventional methods as electric discharge is carried out in the atmosphere. This method has been verified in prior experiments to reduce tool wear through suppression of residual carbon fibers and allow machining in shorter time than conventional EDM.
Through a further series of experiments, a phenomenon where carbon fiber is cut in a safer and lower voltage range than conventional EDM—something that cannot be explained with past knowledge—has been confirmed. It could be due to a compound state that happens through an intermittent combination of electric discharge and partial conducting of electricity.
Currently, in parallel with the development of a processing method that actively reproduces this phenomenon, I am also working on unraveling the mechanism that cuts carbon fiber at low voltage.
Why does the cutting of soft plastics wear out hard tools?
The variety in types of materials are increasing rapidly. In particular, plastic materials are evolving at a blinding speed, and there are many ways to combine them with carbon fiber. CFRP, where the raw materials can be freely chosen according to the application, can be said to be a custom-made material with no standard form. We can say that this is a research field with great hidden potential as there are optimal processing techniques tailored for the respective properties.
Actually, research and development of processing techniques has just started, and I feel my own research has yet to reach even the halfway point. Another major charm of researching CFRP is that its application in the special environment of outer space is advancing. With the space development industry again gaining attention in countries around the world, I think the development of technologies that can help this industry is also an important research theme.
Demand for CFRP is predicted to further expand, such as for applications in next-generation mobility (EV, autonomous driving, and other advanced methods of movement) with excellent energy-saving performance. My future goal as a researcher is to meet the needs of society by focusing on CFRP research using a multi-faceted approach. I also hope to find the answer to the fundamental question, “Why does the cutting of supposedly soft plastics wear out tools which are supposedly hard?”
The book I recommend
“Bunmei no Seitai Shikan”(An Ecological View of History)
by Tadao Umesao, Chuko Bunko
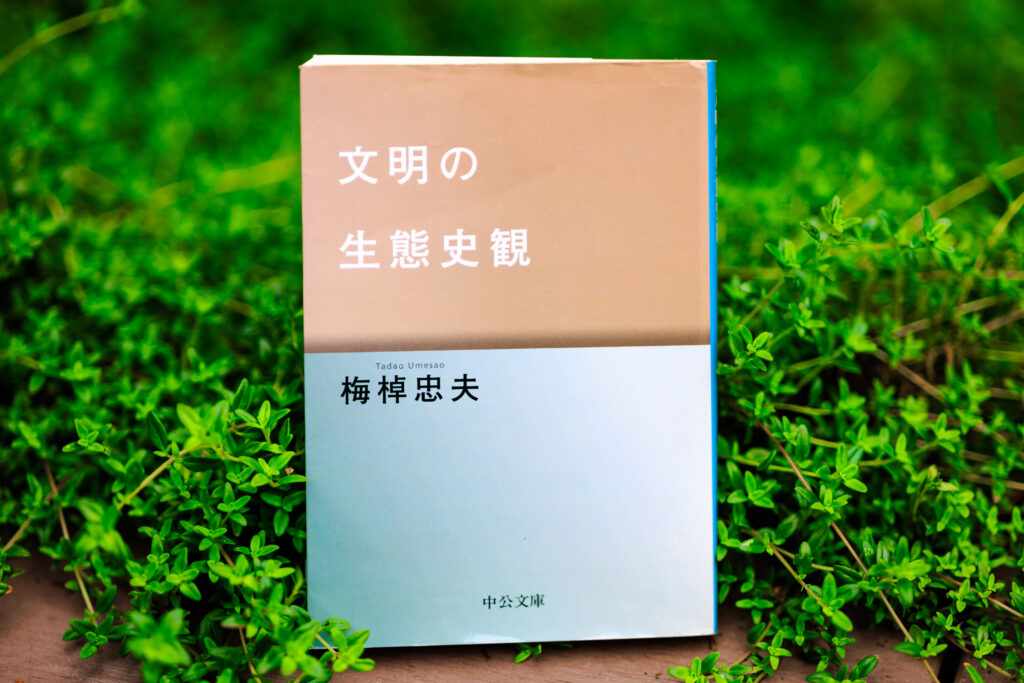
I was deeply impressed by the profound insights from a geopolitical perspective about the reasons behind Japan becoming a developed country as an industrial country. It is a book that I highly recommend to high school students with an interest in manufacturing to understand the psychology of Japanese people toward things.
-
Hidetake Tanaka
- Associate Professor
Department of Engineering and Applied Sciences
Faculty of Science and Technology
- Associate Professor
-
Graduated from the Department of Human and Mechanical Engineering, Faculty of Engineering, Kanazawa University, and received his Ph.D. in Engineering after completing the doctoral course at the university’s Graduate School of Natural Science and Technology. Took on several positions—such as teaching assistant at Kanazawa University’s Faculty of Engineering, researcher at JST Satellite Niigata, research associate and assistant professor for Mechanical Engineering at Nagaoka University of Technology’s School of Engineering, and visiting researcher at Federal Institute of Technology Zurich (ETH Zurich)—before assuming his current position in 2015.
- Department of Engineering and Applied Sciences
Interviewed: September 2023